Key Findings
The U.S. plastics industry is a major contributor to the American economy, supporting hundreds of thousands of jobs. American industry has been a global leader in plastics production, which reduces food waste and improves energy efficiency in transport, compared to substitutes that would be used to perform the same economic function.
Global demand is growing exponentially because of the economic and environmental benefits of plastics. While the environmental cost of plastics mismanagement after use is substantial (e.g., ocean plastics, litter), those costs flow largely from the inability or unwillingness of countries to manage it. The United States can play an indispensable role in helping other economies develop effective waste management policies and advance innovation that can create markets that improve the economics of recycling.
Most importantly, U.S. plastics manufacturers are cleaner from a greenhouse gas (GHG) perspective, compared to China and its main competitors. Ethane, used in U.S. plastics production, has a relatively lower GHG profile than naphtha, which is the primary feedstock in Chinese plastics. Recently proposed U.S. policies have sought to limit plastic production temporarily or permanently in the United States, which would inevitably shift production overseas, likely to China. Not only would this move destroy domestic jobs and reduce the competitiveness of U.S. exports, but it would also have a further adverse effect of increasing global GHG emissions.
The Facts
Plastics, also known as plastic polymers, are a versatile group of materials critical to countless applications and industries—including product packaging, building and construction materials, medical devices, automobiles, and more. This ubiquitous material is created through a process known as “cracking,” whereby hydrocarbons are heated and broken down. Most cracker plants use either naphtha (which comes from crude oil) or ethane (a natural gas liquid) to make ethylene, which is then further processed into a polymer. Depending on the product, several stages of processing may be required before the final plastic is created.
The United States’ shale revolution created an important opportunity for petrochemical companies to pivot towards ethane, helping create plastics more affordably and with fewer emissions. Ethane’s reaction path to create ethylene, the building block of plastics, is shorter than naphtha’s. This shift is notable for reducing the cost of feedstocks and, by extension, plastic products.
Plastic use produces important economic benefits, such as lowering the cost of bringing a product to market. It also helps the environment by improving resource efficiency (e.g., reduction of food waste, water use, and energy consumption). Since its mass production began in the 1940s and 1950s, global demand for plastics has far outpaced demand for other energy-intensive commodities, such as cement and steel. From 1989 to 2020, plastics production exploded from 100 million to 367 million metric tons annually—more than a 250% increase. Packaging accounts for a plurality of plastics demand, representing 26% of the total volume of plastics used.
While increased market penetration of plastics generates environmental benefits, particularly through offset carbon emissions relative to other, alternative materials, there are also notable costs. In a report for the World Wildlife Fund, analysts estimated the total environmental cost to society— including greenhouse gas (GHG) emissions, air, land, and water pollution, water depletion, and ocean impacts—at $3.7 trillion. If current trends continue, these costs are set to double by 2040.
The best-known negative externality is ocean plastics. Reports show that about 11 million metric tons of plastics, the majority of which is packaging, is leaked into the seas annually. At the current rate, that number will increase to 29 million tons by 2040. Studies show that only ten river systems—eight of them in Asia—are responsible for about 90% of the pollution, most of which is Chinese-origin.
Plastic waste management in the developing world is a major environmental challenge. While per capita plastic consumption in richer economies is up to 20 times more than in the developing world, that gap is expected to narrow as incomes rise globally. China accounts for roughly 30% of total worldwide demand today and its share will remain relatively stable up to 2050. Within thirty years, however, Southeast Asia’s share will increase from 8 to 13% and India’s will grow from 6 to 12%—both regions include river systems that are current major pollution sources.
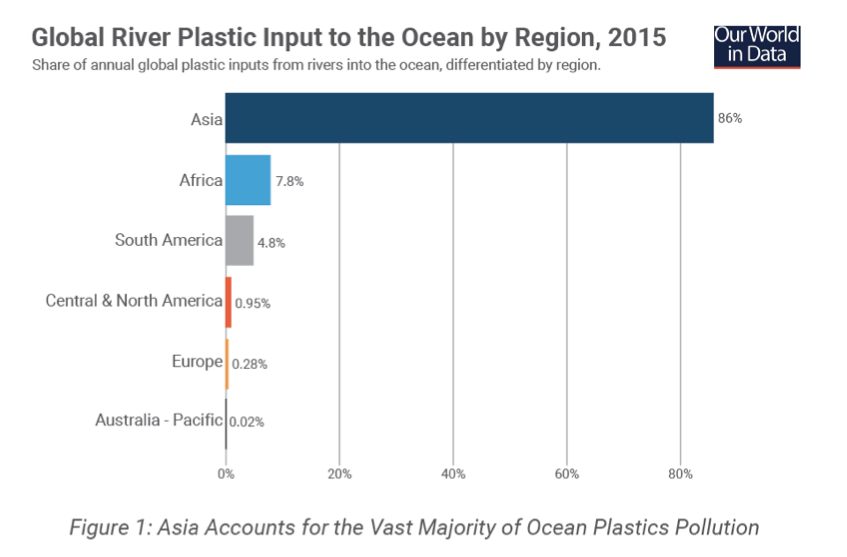
Plastic waste pollution is compounded by low recycling rates. Ninety-five percent of the material value of plastic packaging ($80–120 billion every year) is lost after first use. Only 14% of it is kept with recycling, and when sorting and reprocessing are taken into account, only 5% of the material value is preserved for use again. In general, the overall plastic recycling rate is smaller than for packaging, and both fall short of global recycling rates for paper (55%) and iron and steel (70–90%).
Increased demand for plastics also increases greenhouse gas (GHG) emissions. Over 90% of polymer production relies on fossil fuels, accounting for approximately 6% of global oil consumption (about the same as worldwide aviation). Analysts estimate that plastics are likely to represent 20% of total oil consumption by 2050. The planned buildout of the U.S. petrochemical sector (including upstream and downstream) is expected to increase domestic emissions by more than 180 million metric tons of CO2e by 2030.
The GHG Benefits of Plastic Use
Despite emissions from plastic production, its use avoids GHG emissions on net, largely because its light weight requires less energy to transport, and in the case of food, prolongs shelf life. In fact, research has found that plastic substitutes have a far greater environmental and GHG emissions impact than plastics. In a study conducted by Trucost, for instance, the total environmental cost of plastic use annually ($139 billion) paled in comparison with that of alternatives ($533 billion) in 2015. Moreover, Trucost found that plastic substitution in passenger vehicles sold in North America that year would have increased lifetime fuel demand by about 89 million gallons of gasoline and diesel—$2.3 billion in environmental costs. In a study of plastic packaging compared to substitutes, Franklin Associates estimated that GHG emissions would be doubled by a plastic packaging ban.
More recently, environmental scientist Kenneth Green found that plastics have several environmental benefits over their substitutes, including reduced energy and water usage and a lower carbon footprint. Green also concluded that plastics are still a very young material in the history of material use and that sustainability benefits are still developing. In fact, environmental tradeoffs for alternatives could be greater, which has been found by research by Shelie Miller, an environmental scientist at University of Michigan.
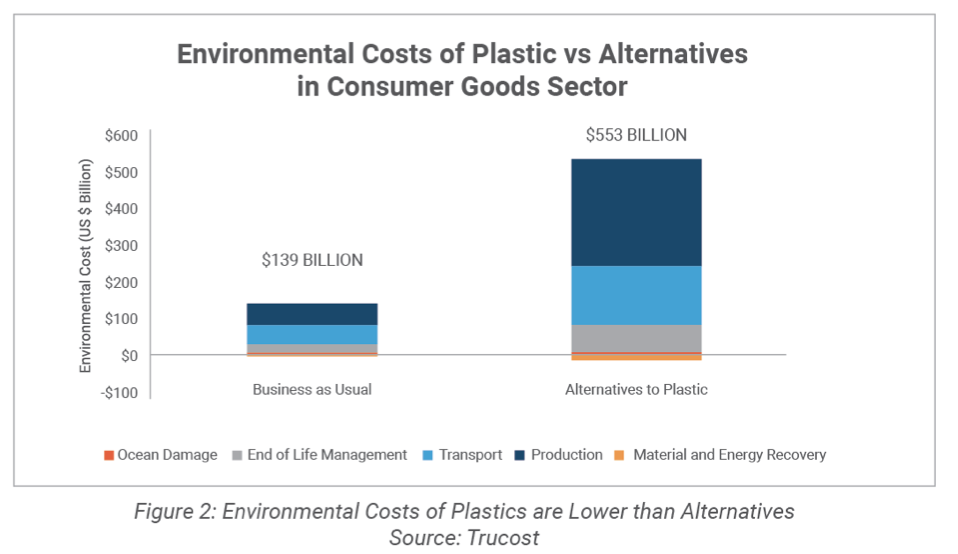
In the case of plastic or non-plastic bags, the environmental impact depends on how many times a bag is reused for shopping or for other purposes, such as carrying garbage. Compared to using a typical plastic grocery bag (i.e., low-density polyethylene [LDPE]) only once, a bag that is made from alternative material has a much higher global warming potential (GWP) because of its increased weight and higher production impacts; while reusing a LDPE only widens this gap. Paper and conventional cotton bags should be reused at least 43 and 52 times respectively to ensure they have the same environmental impact as a LDPE carrier bag used as a waste bag before incineration, while organic cotton bags have to be used 20,000 times, according to a study by the Ministry of Environment and Food of Denmark.

Plastic packaging allows for a higher percentage of food to move from the farm to the market. Accordingly, its use avoids GHG emissions by cutting food waste, which accounts for about one third of all food produced globally. According to the United Nations, if food waste were represented as its own country, it would be the third largest global GHG emitter—behind China and the United States at impacts of producing or optimizing the related plastic packaging—five times higher, according to one study. According to industry sources, cucumbers, bananas, and beef last 11, 21, and 26 days longer, respectively, with plastic packaging.
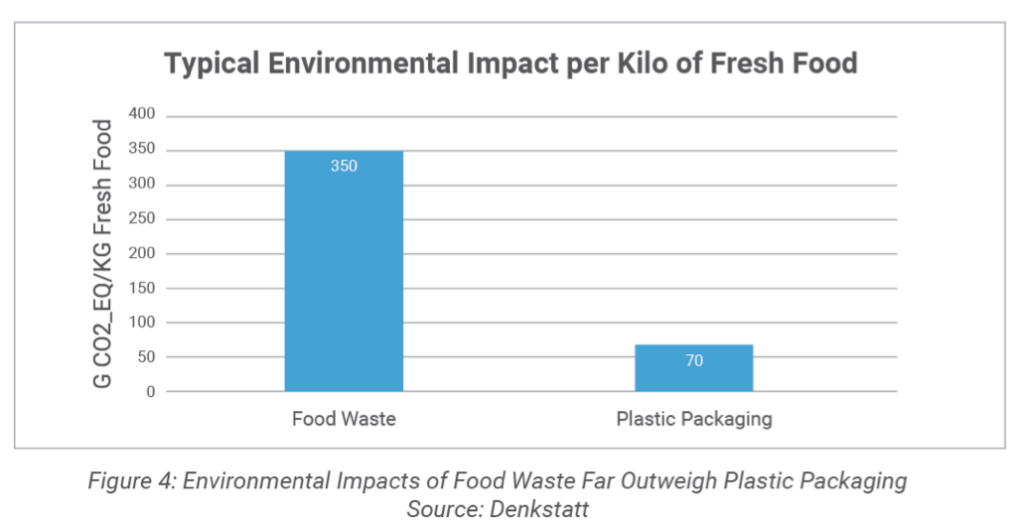
Prevention of food waste also depends on the type of polymer used, which impacts the quality of food that reaches market—e.g., plastic shrink wrapping prolongs shelf life of fruits and meat products. Traditional polyethylene (PE) films, for example, are not as effective at preservation as multilayer films that mix PE with polyamide 6 (PA6), which is more of an oxygen barrier and has greater puncture resistance. As a counterpoint, critics of plastic argue that plastic packaging has incentivized consumers to purchase more goods at once, resulting in unused, larger portions being wasted.
Innovation Key to Reducing Waste and Emissions
Plastic recycling includes three major phases: collecting waste or scrap plastic, sorting waste and then reprocessing that material into useful products. Half of Americans have easy access to curbside recycling, but benefits are limited because not all participate or fail to do so fully, resulting in only a 32% recovery rate for single-family homes. Market conditions, lack of financial support, and inexpensive landfill tipping fees present challenges to expanding collection programs. Moreover, developing a robust domestic reprocessing industry has also proven difficult because a significant percentage of U.S. collected waste has been exported, often times to countries with poor waste management.
In 2017, China—in response to its own waste-related challenges—announced plans to ban imports of 24 types of recycled commodities and to restrict the amount of contamination to below 0.5%. Taking effect in early 2018, its limits were later expanded to include an additional 32 materials.
Because the contamination level for U.S. recycling is between three and five percent, Beijing effectively banned imports of the material from the United States. Shutting off such a huge market (China imported about 45% of global plastic waste since 1992) resulted in a domino effect. Plastic waste imports increased drastically in other parts of the world, particularly in Southeast Asia, inundating their markets. Faced with a collapse of their own recycling infrastructure, a number of additional importing countries moved to restrict shipments from the United States and elsewhere.
As a result of these curbs, U.S. plastic waste exports fell by nearly half between 2015 and 2018—from 2.05 to 1.07 million metric tons. The combination of the de facto import bans and lack of domestic recycling infrastructure placed U.S. cities in a tough predicament. Recycled bails, which once generated revenue, had become a financial burden with local communities having to divert waste to landfills or suspend or cut their collection programs. Consequently, U.S. recycling rates for plastics, which are incredibly low (only 8.4% before the ban in 2017), are likely to worsen before they improve.
The breakdown of the global market for plastic waste, however, is generating demand for more robust American recycling infrastructure, including an expansion of reprocessing. Since 2018, nearly $9 billion in new investment in plastics recycling has been announced in the United States, enlarging capacity and the use of new technologies. Partnerships between industry and government have also become more prevalent. The Houston Recycling Collaboration Partnership, for instance, will reportedly make the city an international hub for advanced recycling and boost domestic recycling levels. Meanwhile, American companies are working internationally to increase recycling, as well as bolstering their investments in the research and development of new innovative technologies. As an example, a new molecular technology in France, pioneered by American chemical company Eastman, will recycle mixed plastic waste, including recycled clothing, to produce new plastic products. Recent drives to finance advanced recycling have proven successful and the emergence of new circular economy-focused companies is widespread. These projects have the potential to divert 6 billion pounds of plastic from landfills.
Continued investment in innovation is required to narrow or eliminate the price gap between recycled and virgin or new plastic, which has grown recently for some polymers. While low oil and gas prices drive down production costs for new plastics, demand growth for recyclables strains existing infrastructure and increases costs. Over 37 of the largest U.S. consumer brands and retailers have committed to use between 20 and 100% recycled content in packaging by 2025. Meeting those targets will require additional capacity overall for recycling and advances in related technologies.
The U.S. Department of Energy (DOE) launched the Plastics Innovations Challenge to create a program focused on accelerating innovations in energy-efficient plastics recycling technologies. The Plastics Innovation Challenge has tapped research capabilities within National Labs, universities, and industry. In October 2020, DOE invested over $27 million in funding for twelve advanced recycling projects, and in May 2021, invested $14.5 million to research and develop new energy-saving recycling technologies for single-use plastics including bags, wraps, and films.
The U.S. plastics industry is also pursuing a number of initiatives that promote a circular economy for some of its products. “Circular economy” refers to a business model in which materials are repurposed instead of being disposed. Mechanical recycling generally retains the original form of used plastics that are sorted, cleaned, shredded, melted, and then re-extruded into plastic pellets, which are then used in new products. The process works for particular resin forms, such as bottles and containers. It also makes plastics for new use, such as pipe, railroad ties, and pallets. However, some plastics are difficult to sort and process mechanically.
To address that challenge, advanced recycling (AR) technologies return plastics to their basic chemical building blocks to create new polymers, which can be used to produce new products. These processes use heat or chemicals to return plastic products to their original building blocks, which can then be reprocessed into complex and high value products, including new plastics (polymers), transportation fuels for aviation and automobiles, waxes for candles and crayons, and other products like synthetic crude oil.
The Importance of Domestic Production to U.S. Economic Security and Global Climate Goals
The U.S. plastics industry plays a significant role in the U.S. economy, directly or indirectly employing about 1.5 million people, which is roughly 1% of the U.S. non-farm workforce. The value of shipments, including those from upstream suppliers, is more than $500 billion. A substantial percentage of U.S. plastics production is exported—roughly 20% of domestic shipments. Compared to other U.S. manufacturing sectors, plastics production alone would represent the eighth largest U.S. industry in terms of shipments.
As discussed previously, worldwide demand for plastics has exploded in recent decades, and overseas markets are expected to expand. Global plastic production reached 8.3 billion metric tons in 2017 and is forecast to grow to 34 billion metric tons by 2050. Capturing a significant share of this future market would bolster U.S. manufacturing, create hundreds of thousands of new jobs, and help maintain U.S. leadership in plastics innovation.
Unfortunately, U.S. manufacturers are losing their share in both domestic and global markets. In 2005, America was the global leader in plastics and rubber production; by 2020, China produced 2.5 times more than U.S. industry. The U.S. trade balance for the sector fell from a $0.7 billion surplus in 2019 to a $5.5 billion deficit in 2020; its largest deficit was over $15 billion with China, which is expected to increase its dominance as the largest exporter of plastics products. This trend certainly poses risks to U.S. national interests and supply chain security, given the indispensable role plastics play in the U.S. economy and its defense, as well as China’s longstanding record of using its economic power to punish governments that take positions contrary to its own.
In addition to the environmental benefits that were discussed previously, U.S. plastics manufacturing compared to most foreign production is cleaner from a lifecycle GHG standpoint. Chinese plastics manufacturing, for example, is nearly three times more GHG intensive than U.S. production. The relative U.S. carbon efficiency of plastics manufacture is largely due to the lower carbon intensity of U.S electricity and its primary feedstock, ethane, which is more climate friendly than naphtha, which is used by Chinese industry. The cumulative GHG emissions for the steam cracking of naphtha is 35% higher than ethane, per kg CO2/metric ton of ethylene (1,135 compared to 840). Accordingly, increasing U.S. industry’s share in global plastics production at the expense of less efficient competitors would reduce global emissions.
The Importance of Ethane to U.S. National Interests
In the United States, the shale revolution and abundance of natural gas significantly increased ethane supply, driving down ethane’s price and the cost of “cracking” it into ethylene, particularly in U.S. regions with an abundance of wet gas (e.g., Marcellus). As a cracker feedstock, ethane has great appeal—its reaction path to produce ethylene is much shorter than naphtha, the yield higher, and the production cost lower. Accordingly, U.S. ethane production rose 210% between 2011 and 2021. America is the world’s largest producer of ethane, holding a 32% market share in 2019—compared to 27% only two years before. U.S. industry is expected to add nearly one million barrels per day (b/d) of new ethane supply before 2030—more than a 40% increase; at the same time, Saudi Arabia, the world’s number two producer, will contribute another 222,000 b/d.
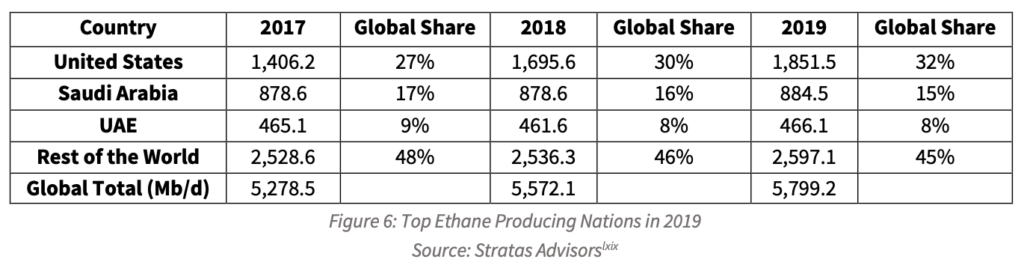
The mix of petrochemical feedstocks varies from region to region, largely contingent on the relative availability of natural gas liquids and oil. Wet gas-rich regions in North America and the Middle East enjoy a cost advantage with ethane. European and Chinese producers depend on naphtha, which is generally more expensive, but that cost gap narrows during periods of low oil prices.
With fuel, power, and chemical feedstocks accounting for 70% of manufacturing costs, even small cost reductions enhance competitiveness. Domestically, investment has poured into petrochemicals since 2010 with completed, under construction, or planned projects totaling more than $230 billion. Today, at least 25% of U.S. cracking capacity is comprised of ethane-only crackers, and the sector is generally expected to continue its ethane reliance. While U.S. petrochemicals are currently competitive in global markets, that advantage may erode over time as domestic consumption and global demand for U.S. ethane drives domestic feedstock prices higher.
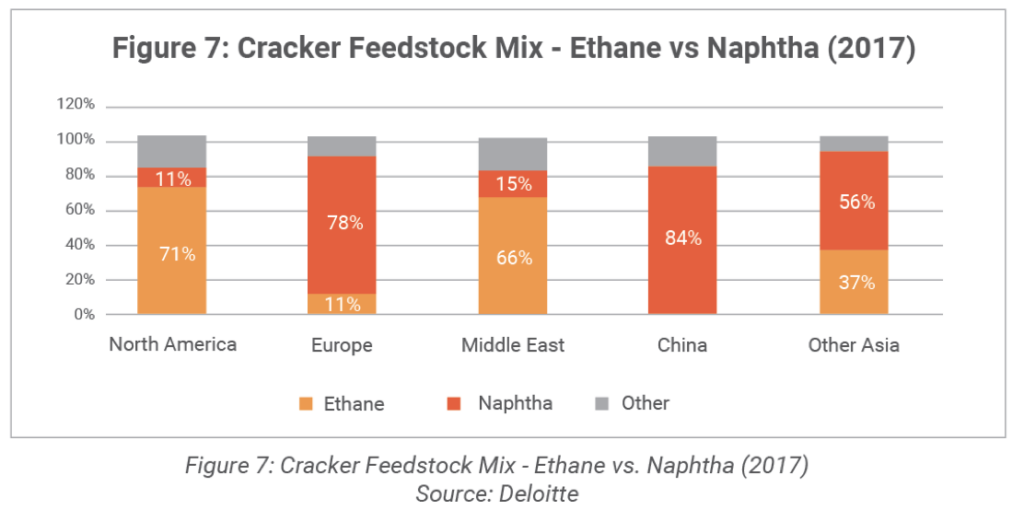
Despite the number of ethane producers worldwide, the United States is one of only two countries that exports the feedstock. U.S. ethane exports grew from almost zero in 2013 to an average of 260,000 b/d through the first ten months of 2018, representing roughly one-sixth of U.S. hydrocarbon gas liquids exports. In the first few years, U.S. ethane exports were sent only to Canada, but by 2018, shipments had expanded to at least 10 countries. Analysts anticipate that U.S. dominance of the ethane export market is likely to remain in the foreseeable future. Few countries will have sufficient excess ethane available to underwrite construction of capital-intensive export infrastructure.
Chinese industry is seeking to secure long term U.S. supply, highlighting ethane’s importance as a strategic resource. The United States began exporting ethane to China in 2016, and now has three terminals in operation; one near Philadelphia, PA and two near Houston TX. China has been the largest buyer of U.S. ethane since January 2021 when operations began at the third terminal, the Orbit Ethane Export Terminal, which is owned by U.S. company Energy Transfer in partnership with the U.S. subsidiary of Zhejiang Satellite Petrochemical. While Chinese purchases would benefit domestic producers of ethane, American policymakers have increased scrutiny of natural-gas liquid exports, with Senators Joe Manchin (D-WV) and Debbie Stabenow (D-MI) launching a probe of Russia-backed company American Ethane’s contracts with Chinese buyers in 2019 over national security concerns.
China certainly intends to dominate the global petrochemical industry; it already accounts for roughly 40% of the sector’s global revenue. Investments in the country’s production capacity are expected to account for 27% of global growth from 2019 through 2030.
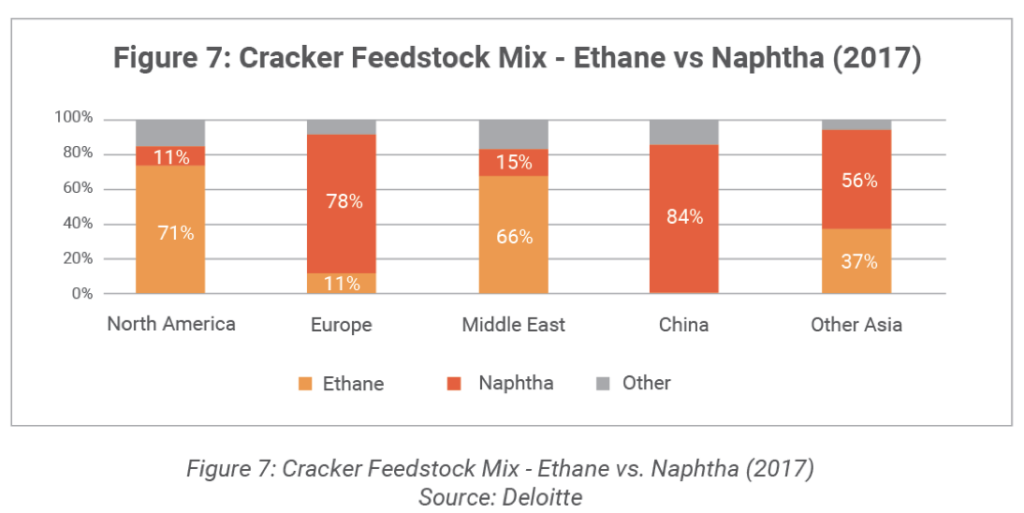
Given its relatively lower GHG profile than naphtha, ethane’s value would increase if major economies moved forward with plans to tax or charge fees on imported products based on their carbon intensity. As governments seek deeper reductions in GHG emissions, momentum is gathering in the European Union (EU), the United States, and elsewhere to level the playing field for domestic industry that faces greater carbon regulation than their foreign counterparts.
EU and U.S. policymakers have independently introduced legislative plans that would merge climate and trade policy, particularly impacting energy-intensive manufacturing sectors. Last July, the EU proposed a Carbon Border Adjustment Mechanism (CBAM), which would mandate reporting of carbon content of covered products. Its full adoption would require most importers to pay a carbon fee or tariff at the EU border on commodities, such as steel and aluminum. Within days of the EU CBAM announcement, U.S. Senator Chris Coons (D-DE) and U.S. Representative Scott Peters (D-CA) unveiled the FAIR Transition and Competition Act. Their plan would include the same sectors as the EU CBAM, as well as the import of fossil fuels, including coal, crude, and natural gas.
While current proposals do not cover petrochemicals, the scope of climate and trade regulation is highly likely to expand to include the sector and eventually, even more narrowly, to plastics production. Such a development, particularly if it occurred within the context of a plurilateral agreement between the United States, the EU, and other developed economies, would increase the competitiveness of U.S. plastics-related exports relative to Chinese naphtha-based exports, reducing global emissions linked to plastics production as China’s goods were displaced in the marketplace.
If bolstering American manufacturing and reducing worldwide greenhouse gases are priorities, U.S. policymakers should consider the climate and trade policy trajectory when determining the approval of U.S. ethane exports, particularly to China. Allowing China to lock in long term U.S. ethane supply while expanding its petrochemical capacity would only place the United States at a competitive disadvantage.
The Problem with Current U.S. Policymaking
Regrettably, a growing number of U.S. elected officials and environmental groups are calling for policies that would severely obstruct the ability of the U.S. plastics industry to compete in the domestic and global marketplaces—supposedly in the name of addressing global climate change. Proposals that are currently being tabled would result in increased plastics imports, destroying U.S. jobs—thousands of which are located in battleground states. Ironically, from a climate mitigation perspective, their policies, if implemented, would result in an increase in global greenhouse gas emissions as more carbon-intensive overseas production filled U.S. domestic and international demand.
The Climate Leadership and Environmental Action for our Nation’s (CLEAN) Future Act, approved by the House Energy and Commerce Committee in 2021, for example, would impose new clean air permitting requirements on industrial plastics facilities. Specifically, the Act calls for the Environmental Protection Agency (EPA) to enforce “a temporary pause on new permits for facilities that produce plastics”—a process that would undermine new investments in related U.S. manufacturing. This “freeze” would certainly last for at least months (in a best-case scenario) and potentially create the conditions for an “indefinite moratorium” on new U.S. plastics facilities, helping hand global market growth to more carbon-intensive Chinese production.
Worse yet, the Break Free from Plastic Pollution Act of 2020 with nearly 100 cosponsors in the U.S. House of Representatives would impose a three-year moratorium on new permits for domestic plastics production and then require U.S. manufacturers to manage the recycling and recovery of plastics once they are used. While the plastics industry has tentatively supported some similar programs, a blanket shifting of the environmental burden onto producers often can fail to acknowledge the real market challenges to U.S. recycling efforts, as discussed previously. These hurdles require a much more comprehensive approach that largely falls outside the ability of U.S. plastics producers to control. Perhaps, more importantly, it fails to acknowledge the economic and climate benefits that plastics provides. If adopted, plastics substitutes that result in greater environmental damage would become more competitive in the marketplace.
While plastics use clearly creates challenges, the U.S. policymaking community needs to pursue a pragmatic approach based on facts. First and foremost, multiple studies and research across multiple continents indicate that plastics are superior to substitutes when it comes to economic and environmental performance. Not surprisingly, global demand for plastics will continue to expand significantly because of market forces. Second, waste management presents market challenges, but those are mostly in overseas markets that are increasing plastic use but suffer from a lack of enforcement and compliance regimes. Global recycling rates need drastic improvement, but addressing that problem depends largely on the ability of U.S. plastics producers to innovate and develop solutions that can be exported overseas. Lastly, U.S. plastics manufacturing is amongst the cleanest in the world from a GHG perspective. Pursuing any policy that undermines U.S. competitiveness domestically or internationally would result in increased worldwide environmental and climate costs as dirtier foreign, particularly Chinese, production meets global demand.
Conclusion
Discussions on the environmental impacts of plastics must consider two important facts about GHG emissions: plastics often have a lower emissions profile than current alternative materials and the use of ethane in the United States to produce plastics emits relatively fewer emissions than naphtha- based production in China or elsewhere. Attempts to curb plastics production in the United States on the basis of reducing emissions would ultimately have a paradoxical effect of increasing emissions globally through a larger share of plastics produced in China using naphtha as a feedstock.
Plastics, already vital in the global economy, will grow in importance as incomes rise in developing nations. Although some related environmental impacts are highly visible (e.g., ocean waste) and related costs are significant, increased plastic use presents opportunities to address greenhouse gas (GHG) emissions; for example, it reduces food waste and improves energy efficiency of transport. It is also generally cleaner from a GHG perspective than its more energy-intensive alternatives, such as aluminum, cardboard, glass, and wood.
Of course, plastic waste should be addressed. In the past, richer economies simply exported a majority of their collected waste to other countries, especially China, which lacked effective waste management. The financial side of that arrangement changed when Beijing, which bought about half of the world’s plastic waste, enacted an import ban to better control its own problem and create a larger domestic market for its own virgin plastics production. Now, the economics have improved for U.S. recycling programs, creating a more conducive environment for American innovation.
U.S. plastic producers are responding to greater consumer demand for recyclables and have pledged to move forward with a “circular economy” for plastic packaging—meaning that these products will all be recovered, recycled, and reused. Meeting that target will require greater investments in existing recycling technologies, as well as breakthroughs in advanced recycling, which is needed to handle plastics that are more difficult to sort and process.
U.S. recycling innovation is also critical for reducing global plastic waste. While bolstering waste management in developing countries is needed, existing recycling technologies cannot solely cope with the problem. Innovation in advanced technologies is required to further improve recyclability.
In the likelihood of merging climate and trade policy where plastics are “priced’ by their carbon intensity, U.S. production would gain a competitive advantage because of its reliance on ethane, increasing America’s global market share in the plastics. Accordingly, U.S. policymakers would be wise to ensure that foreign purchases of ethane and associated assets do not restrict the ability of domestic petrochemical producers to compete in domestic and global markets. Moreover, legislators and environmental activists should understand that U.S. plastics production is not the problem—it is actually the answer to addressing global GHG emissions, particularly if it displaces dirtier overseas production.
APPENDIX:
Table 1. Common Materials and Polymers, U.S. Recycle Rates for Containers (total is usually less)
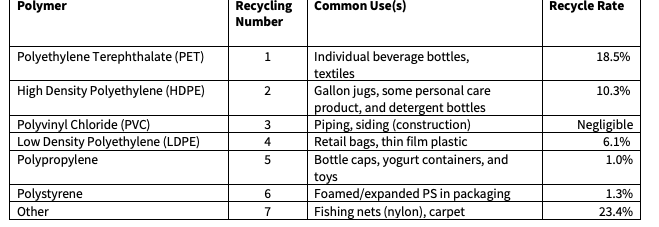
Table 2. Highly Recycled Items in the U.S. and Potential Reasons Why
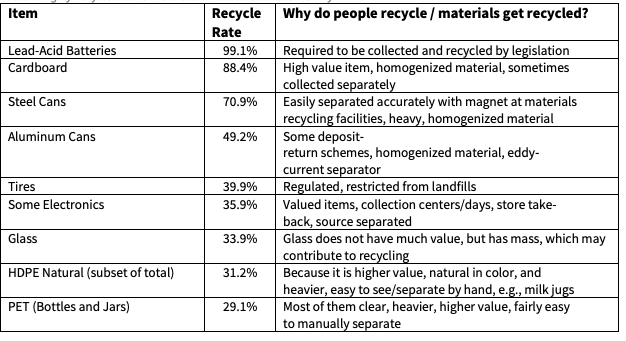